The Combinations | Custom Solutions
Our Custom Solutions Gallery highlights details and photos of the particular ramp and/or platform, along with a brief commentary on what the customer wanted to accomplish.
The Challenge:
One of our mobile yard ramps in circulation sustained damage: The support crossbeam connector brace under the ramp was bent, sustaining damage during a repositioning, which compromised the integrity of the support legs and wheels. The hand-crank gear box was stripped and the crank handle broken and torn. The short term for this is “user abuse.”
The Approach:
Through our network of turnkey service partners, we contracted a worthy welder. We confirmed with both welder and current renter a date and time. We secured the delivery of replacement parts.
The welding team first removed the compromised leg assembly and connector brace from the ramp. The team then spot welded the new leg assembly and new connector brace. The team applied a comprehensive weld. The customer tested the integrity of the job through a repositioning of the ramp.
The Results:
The yard ramp is now returned to its strong, intended integrity. The new hand crank mechanism raises and lowers the leg assembly smoothly. The new connector brace is straight. The yard ramp is again a strong, safe piece of equipment that will offer many more years of use.
Read more about it HERE.
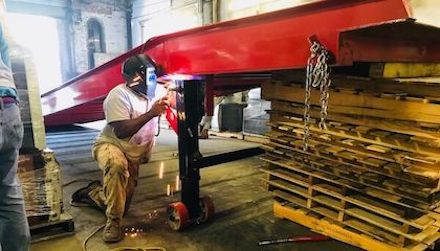
Custom Solutions to Streamline Your Process
The Challenge:
Our customer, a California developer, had begun renovation of a 600,00 square-foot refrigerated and dry-storage warehouse. With all entryways dock-high, he required an extra wide high-capacity ground-to-dock yard ramp for accommodating material handling equipment entering the facility.
The Approach:
Based on the developer’s own drawings, we contracted with our manufacturer for the construction of a 10-foot-wide, 80K-lb capacity yard ramp with stationary legs (projecting that future tenants will utilize the ramp throughout the lease/purchase).
The Results:
The manufacturer crafted the yard ramp as per specifications. Delivery: on time. Customer’s welder positioned and installed the ramp to the dock the following day in two and a half hours.
Read more about it HERE.
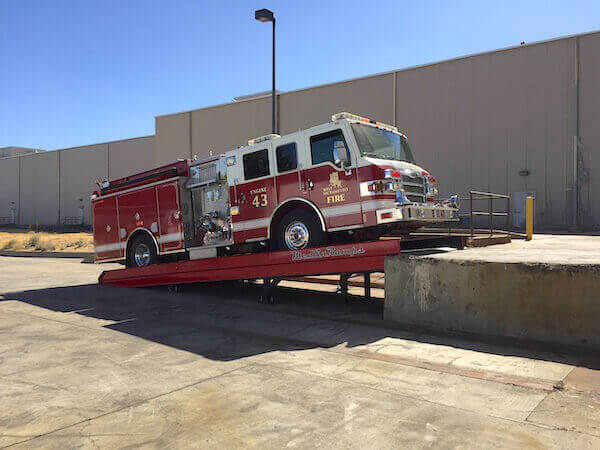
(Ample) Proof of Capacity
The Challenge:
A potential customer in Texas who manufactures specialty vehicles had been commissioned for a customized golf cart in the shape of a baseball hat for delivery to Seattle. She needed a way to put the cart into a truck and was reluctant to use a forklift because she didn’t want to damage the cart.
The Approach:
The total time needed for a yard ramp, at both ends, would be about two hours. We did the math, and total cost would be some $2,800. While we frequently engage in short-term rentals, both the customer and The Yard Ramp Guy agreed that the price was quite steep.
Given that situation, we still don’t like to say “no.” We brainstormed on the idea of her hiring a handyman to custom-build a pallet to accommodate the cart, with a small wood ramp that would allow a forklift to lift the entire platform onto a truck.
The Results:
She had the platform built (total cost: a few hundred dollars). The specialty cart was loaded in Texas and off-loaded in Seattle without a scratch.
The Yard Ramp Guy’s approach: we help the customer develop better ideas, which leads to better relationships. When the time is right for us to do business, we’ll do business.
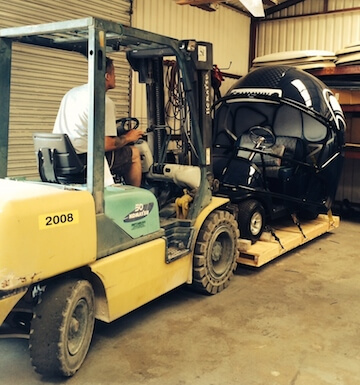
Building an Alternative Mousetrap