Note: Greg Sanders from Crom Weld approached us a few weeks ago about a guest post. We appreciate his can-do spirit and the really helpful nature of his website, which provides a great resource for the welding community.
That initial discussion grew into this two-part series, graciously written by Greg. It provides a drilldown to the very weld that determines the integrity of a yard ramp. Greg demonstrates a commitment to the details, which matches the foundation of our own business model.
While we’ve profiled the importance of good welding in a previous blog, we heartily welcome and appreciate Greg’s particular expertise.
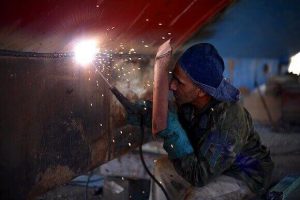
Steel yard ramps allow you to move cargo easily from the truck to the loading dock door with a forklift. They are extremely strong, built to withstand inclement weather and heavy loads when loading and unloading shipments from delivery trucks, containers and railcars. Many are portable and, because they’re made of welded steel, they require very little maintenance.
Stress and fatigue failures usually happen suddenly and can have catastrophic results. Quality manufacturers — like those The Yard Ramp Guy works with — let you know, of course, about what to look for and how to properly maintain your ramp.
What to Look for During Inspection
For any company or industry that relies on the use of portable steel yard ramps, an annual inspection — or more often, depending on use — should be conducted under good lighting.
If done correctly, a visual inspection can be an extremely effective method of maintaining the ramp as a whole. Keeping an eye on weld integrity is an important part of this. Two particular things to look for are:
- Corrosion and Oxidation. Rust is natural. It’s always going to exist. However, a high degree of corrosion on the weld itself could indicate a failure of the weld design, welding practice, contamination from moisture, porosity, or incomplete weld penetration. It is a sign that further investigation is needed to be sure that the weld integrity has not failed.
- Cracks. Welders normally catch cracks during the welding process, but cracks don’t always appear immediately after welding. They can develop over time after the weld has been subjected to loads while in service. If you see them in the inspection process, they need to be taken care of immediately.
What Could Cause the Problems
While it rarely occurs, if there is a problem with the yard ramp, it will likely be due to either
- a defect in the weld, or
- excessive load or stress over the rated ramp’s capacity.
Most manufacturers strive to ensure that their production process and the quality of their welding is flawless, but there are those occasions where the process breaks down and the weld operator does not properly clean the metal he’s about to weld or take enough time to ensure the weld fuses properly.
While truck or rail operators are well versed in yard ramp safety standards, sometimes they hurry to get materials loaded or unloaded and overload the yard ramp.
Both of these situations create stress on the joints and weld lines in the yard ramp and could ultimately result in the weld cracking, buckling, or breaking.
Next week: how to spot weld defects and prevent compromising the integrity of them.
__________
Greg Sanders is the owner of Cromweld.com, a website devoted to all things welding. Greg is semi-retired from welding but likes to keep learning, as well as sharing his knowledge through his website. You can also find him on Facebook and Twitter.