Note: Last week, our guest blogger and expert welder Greg Sanders from Crom Weld wrote about welding practices—what to inspect to assure integrity and to be preventive. His terrific insights are specifically targeted at yard ramps; we’re fairly certain they apply to the majority of industrial equipment employing welds.
This week, he concludes with how to spot weld defects and maintain their integrity. We’re honored to provide space for Greg in this forum.
Toward the Safety and Integrity of Your Yard Ramp
Defects in the Weld
A number of factors can contribute to a weld having initial defects. Some are the result of the metal used, and some indicate the weld itself wasn’t done well.
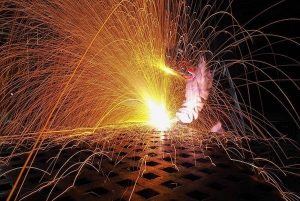
- Cracking can occur due to excess hydrogen, stress level on the weld, high carbon content in the base material, or a concave weld surface. Cracks might be at the toe of the weld, along the centerline of the weld, or at other points.
- Inclusions can occur when the weld metal is contaminated on the surface of the joint due to improper cleaning between weld passes. Slag forms in the flux used in the welding process and can be trapped in the metal while it solidifies.
- Undercut is where the thickness of the steel sheets is reduced at the toe of the weld. During the final weld pass, the exposed edges of the weld can have a tendency to melt down into the deposited filler metal in the weld groove, resulting in sharp edges along the weld reinforcement. Undercut develops because of improper welding techniques, incorrect voltage settings, travel speed, and incorrect electrode angle.
- Lamellar tearing is a problem wherein the rolled steel plates are made of inferior materials with high sulfur or hydrogen content. After welding, shrinkage forces the faces of the plates to pull apart.
- Porosity (otherwise known as pinholes) happens when gases become trapped in the weld metal as it solidifies. These may arise from damp tools or metal or from dirt, oil or grease, on the metal in the area of the weld.
- Lack of penetration occurs when not enough filler weld material has been laid into the weld joint so the weld does not go deep enough.
- Lack of fusion. MIG welding employs a gun that moves wire through it at a certain speed, with a shielding gas to keep out contaminants. The end result is fusion: melting and combining the base metal with filler material to create a joint that’s as strong as or stronger than the original metal. Lack of fusion occurs when the voltage or wire speed is set too low or the operator’s travel speed is too fast.
Ongoing Use/Stress
Whether welding just a few simple parts or manufacturing large, complicated structures, weld fatigue is a very common failure when parts or structures are subjected to heavy loads. Estimates suggest that 90% of failures in steel structures are due to stress and fatigue.
- Weather. Dirt turns to mud in the rain. Steel generally withstands dramatic changes in temperature and weather. Most portable yard ramps include a serrated grating (and all of The Yard Ramp Guy’s inventory has serrated grating), which provides excellent traction for forklifts. The open design allows water and debris to pass through instead of pooling. If the weld is not tight, water can get between the metal pieces at the joint and over time create a stress fracture.
- Rated Load. If the ramp is used over its capacity, it obviously will weaken. If you factor in weight on the wear and tear of different components (wheels, ramp clamps, etc.), less is always more. That’s unlikely because you’d probably be tipping overloaded forklifts long before damaging the ramp. Many forklifts run 6,000-9,000 pounds and can carry 50%-75% of their weight; that’s 9,000 to 16,000 pounds going up and down the ramp. Steel ramps are solid and typically can hold up to 25,000 pounds.
- Movement. This isn’t normally a big issue for welds. Still, since businesses move portable ramps often and on a variety of yard surfaces, some jostling can occur that might stress welds that are otherwise weakened already.
Conclusion
Along with quality metal, cut to precision, the welding gives the yard ramp—and the manufacturer, and the dealer—its strength and integrity. Knowing the basics of how to inspect for welding defects and why they happen, a manufacturer can properly oversee and managed the welding process to prevent welding defects from happening in the first place.
Keeping your eyes open for excessive rust or cracks along welds can help you take preventive steps before the point of catastrophic failure.
__________
Greg Sanders is the owner of Cromweld.com, a website devoted to all things welding. Greg is semi-retired from welding but likes to keep learning, as well as sharing his knowledge through his website. You can also find him on Facebook and Twitter.